Electric vehicle manufacturing trends in 2025 :The game changers
Identify the top manufacturing trends that would shape an electric vehicle successful in the year 2025
Electric vehicle manufacturing trends in 2025 :The game changers
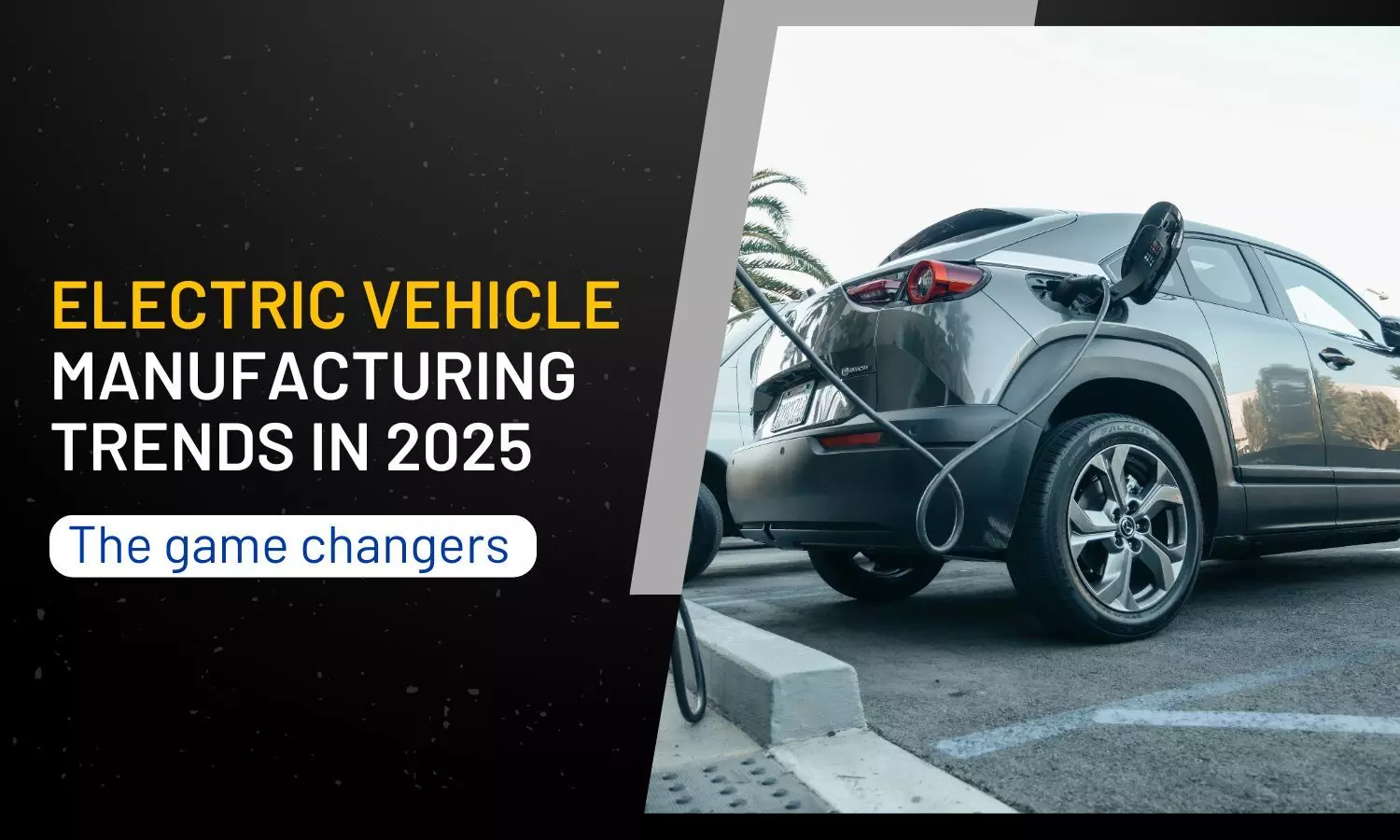
The electric vehicle (EV) industry is growing exponentially, with new advancements in production expected to disrupt the way vehicles are manufactured. Looking ahead to 2025, there are a number of relatively defining trends in the manufacturing of EVs that will impact the industry overall. These technological leaps are not just enhancing the efficiency, affordability, and volume of output but also making sure that the EVs stay relevant in the growing demand.
1.Digital Twins – The Game Changer in EV Production
By the end of 2025, digital twins, which are virtual versions of physical assets or systems, should become a common technology in the automotive industry. In EV production, digital twins allow manufacturers to visualise simulations that can further optimise the assembly lines as well as the battery integrations. This accompanies the digitalisation of many manufacturing tasks, allowing for forecast based management of manufacturing that limits wastes before they occur.
Batteries have now become an integral part of electric vehicles but integrating them into the EV platforms is still a huge challenge for the manufacturers. With the aid of digital twins, the battery manufacturer can visualise the entire battery assembly process and look for issues like, misalignments, inefficiencies, or challenges regarding thermal management. In such cases, real-time changes can be made to precise operations so that there is minimal room for error, hence increasing the speed of the process.
The utilisation of digital engineering in the digital twin lifecycle is set to rise exponentially in 2025 and beyond. Manufacturers will increasingly begin to fuse advanced engineering approaches with these virtual models to gain greater perspectives on production systems and boost the quality of what is being produced. The universal viewpoint of the Digital Twin Consortium has already got the green light to incorporate advanced engineers’ techniques in different industries.
2. Advanced Robotics: A Transition from the Drill Press on to the CAD System
Robotics has played a crucial role in the automotive industry for quite some time now, but looking ahead, in 2025 Complex robotics will begin to have a new paradigm. People always picture a traditional robot as one that is able to only perform a repetitive task with accuracy as that’s what most traditional robots were designed for. Going forward in EV manufacturing, robots will be much more intelligent, adaptable, and will be able to work with human counterparts.
As employment progresses, one quite a significant change that stands out amongst the rest is the rise in the quantity of collaborative robots or cobots that help sort through delicate tasks alongside human workers for example, where cobots can assist in the assembly of aluminum frames or wiring harnesses, which in turn are crucial components in EVs that need both care and finesse. It goes without saying that these sorts of cobots will also include advanced AI software and sensors to allow for safe and efficient collaboration between the robot and a human worker thus preventing mistakes and enhancing productivity.
Also, autonomous mobile robots will improve the efficiency of material flows inside the EV plants when handling parts in particular. Those sorts of robots are capable of moving components from one workstation to another all by themselves which minimises the time gaps that occur when waiting for one element to be carried to the next workstation and thereby optimising the entire production cycle. As the number of cars on the roads will soon increase dramatically, the balance, and control of smooth and accurate material movements will soon become an important factor in maintaining the pace of production lines with quite strict deadlines.
3. AI Systems in the Relevant Area: Improving Precision Strategies while Decreasing Costs
With the amount of competition that exists in the EV market, quality control does not come as important but rather quite a crucial aspect. This will also rely on the fact that more and more electric manufacturers will operate under the Automotive Core Quality Standards requiring the production of vehicles that meet strict guidelines for safety, reliability, as well as performance, whereby, in 2025, AI-controlled quality control systems will already start becoming commonplace in the process of making electric vehicles.
Computer vision and machine learning-algorithms based AI systems will perfect their role in spotting defects and irregularities in the production process. Whether it is looking for molar cracks on battery cells or determining whether the welds on aluminum frames are of required quality, AI will assist manufacturers to take precautions against such unfined defects. This degree of accuracy helps to mitigate the chances of incurring hefty expenses as a result of product recalls as well as improving the level of satisfaction of the customers in the sense that only the best vehicles go to the market.
Furthermore, it will be possible for systems driven by Artificial Intelligence to notice abnormalities within the data of the production, warning signs before interferences operate. In this way, by taking corrective actions to manufacturing aberrations, the overall quality of EVs can be improved, wastes minimised and supply chain management can be enhanced.
4. Sustainable Manufacturing – Greening the EV Supply Chain Management
Given the growing threats EVs pose to the environment, manufacturers will increasingly seek to make the necessary EVs in a manner that is not harmful to the environment. Sustainable manufacturing practices will be one of the major trends in 2025, with lens on energy efficiency scopes and utilisation of renewable energy in plants.
EV plants will incorporate closed-loop water systems, energy-efficient tools and solar energy in their manufacturing lines to reduce ecological pollution. There will also be a stronger emphasis on circular manufacturing processes which advocate for reusing parts of end-of-life vehicles in new vehicles. For instance, reusing lithium from old batteries to manufacture new electric vehicle batteries contributes to the resources conservation principle.
At the same time, engineers will focus on better lightweight composites, and recyclable battery parts to enhance the net environmental effects of the EV while also lowering the manufacturing cost. The industry will also not only be growing, but more importantly, will be growing in an environmentally friendly manner with an efficient and circular supply chain.
Conclusion: The Future of EV Manufacturing in Their Connected, Smart and Sustainable Way
The growing electric vehicle market will mean that the manufacturing technologies of 2025 will have to be emphasised if the industry is to succeed. Emerging technologies, such as digital twins and AI-driven quality control systems, advanced robotic systems, and sustainable practices will enable EV makers to manufacture vehicles that are high quality and cheap, as well as being environmentally friendly. With these trends, manufacturers will be able to deal with the shifts that are afoot in the automotive industry and position themselves well in global competition for the electrification of the automotive industry.